Indium mirror coating system
Author: Senior Manager, Technical Development Dept. Hikaru Kojima
Indium mirror coating system
New development In. Mirror Coating System
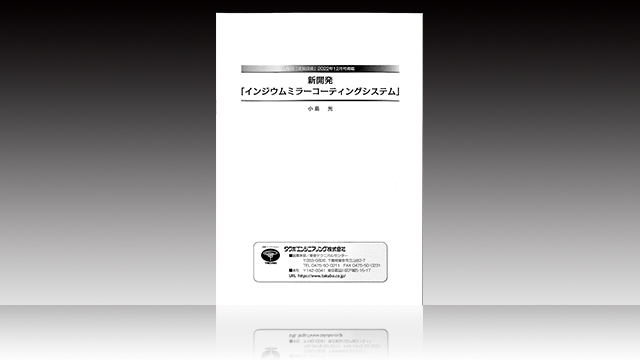
Introduction of the In. Mirror Coating System, a mass production system for plating-like coating, and ECO MIRROR 49, an indium paint.
New development “In. Mirror Coating System”
Plating and vapor deposition are known as means of imparting mirror-like surface designs, but plating has a high environmental impact in terms of wastewater treatment, etc., while vapor deposition requires extensive and costly equipment and cannot be produced in continuous lines because it is a batch process. To solve these problems, various plating-like coatings have been developed, but it has been difficult to deploy them for industrial use due to problems with coating technology and cost. The joint development of Musashi Paint Holdings Co., Ltd. and Takubo Engineering Co., Ltd. has made it possible to realize the mass production of plating-like coating by spraying. This paper introduces the “Indium Mirror Coating System”, a mass production system for plating-like coatings, and “ECO MIRROR 49”, an indium coating.
1. Why Indium Now?
As shown in Table 1, the history of mirror coating systems began with the first generation of silver mirror coatings (silver nitrate reacted with ammonium) and continued with the second generation of silver colloids and silver complexes, but it was difficult to develop any of these for industrial use due to problems of weather resistance, corrosion resistance, and the unit cost of the coating. This led to the birth of the third generation of indium paints, which excelled in weather and corrosion resistance.
However, indium, like silver, is expensive, so the biggest challenge was reducing paint consumption to popularize it for industrial use.
In order to solve this problem, "rotary coating with R technology," which combines high productivity and high quality with less coating material, became indispensable, and Musashi Paint Holdings and our company entered into a business alliance. To be "an alternative to plating and deposition," the cost of paint and coating is critical.
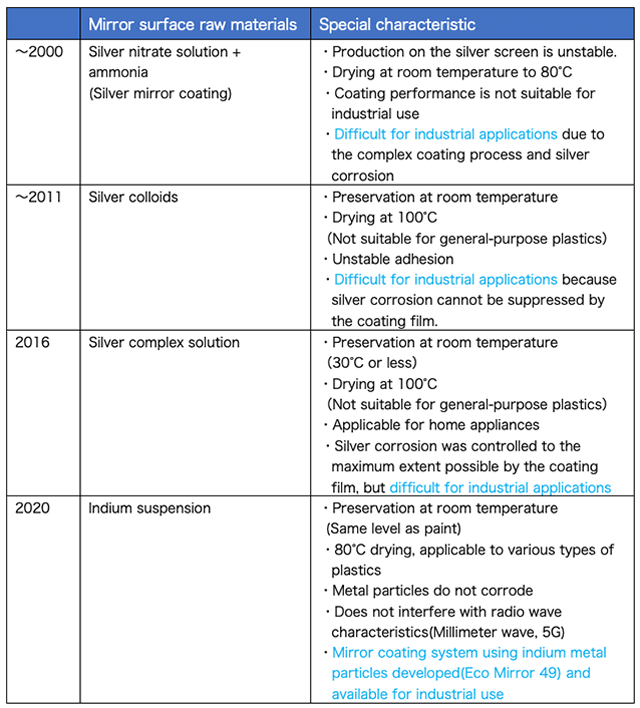
2. Features and applications of indium paint
Indium in indium paint is a rare metal with atomic number 49 and the element symbol "In.
It is a soft, silvery blue-white metal that is stable at room temperature.
Once produced in Japan, it is now almost exclusively imported from China.
The name "indium" is said to have originated from the color indigo blue in the emission spectrum. It is an easy-to-handle metal with a low melting point, conductive and permeable, and its thin film has rare characteristics in metallic coatings of transmitting millimeter waves, etc.
In recent years, radio wave permeability as well as mirror surface design has been required for the chassis of cell phones, electronic devices, information terminals, and automobile parts (front grilles, bumpers, etc.). Cell phones, electronic devices, and information terminals have communication antennas, etc. inside the housing and must have radio wave permeability. In addition, antennas for various radar devices such as distance measurement are installed near the front grille and bumper of automobiles, which must have radio wave permeability. The radio wave permeability around the antennas has a significant impact on radio wave reception performance.
The features and applications of indium paint "ECO MIRROR 49" are shown below.
- Spray coating to achieve a mirror-like appearance.
- Suitable for a wide range of substrates in the low-temperature range (80°C), and not selective to materials.
- Variations are available by changing the topcoat. (See Photo-1)
- Various mirror surfaces such as "glossy," "matte," and "colored" are available.
- Because of its superior weather and corrosion resistance, it can be used for automotive exterior parts that have been difficult to introduce in the past.
- Excellent radio wave permeability makes it suitable for automotive security and safety applications. (See Figure 1)
- All products/items requiring existing "plating" processing treatment are eligible. (Automotive interior and exterior parts, emblems, door/window knobs/keys, eyeglasses, IT equipment, etc.)
Wide variety of design coatings
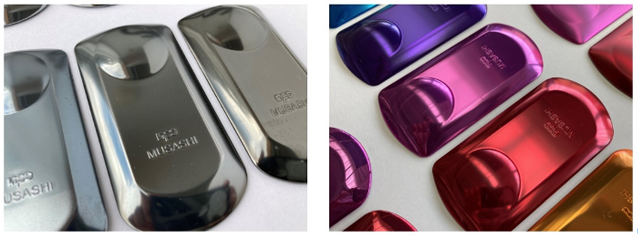
Millimeter wave transmission image
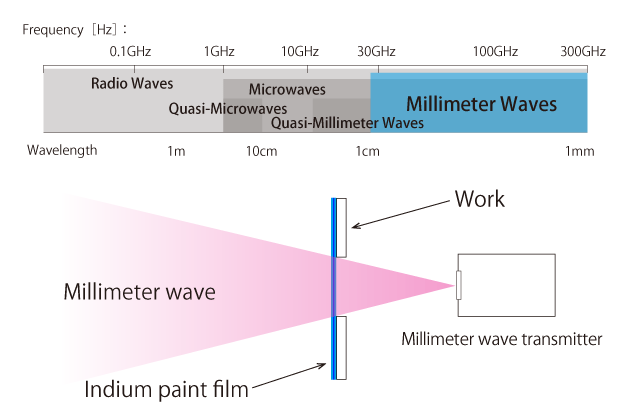
One of the radio wave characteristics required for automobiles is obstacle detection radio waves used in vehicle driver assistance systems. The front of the car requires advanced detection performance, so radio waves in the 76-77 GHz band are emitted, while the rear of the car emits in the 24 GHz band.
The results of the measured radio wave transmission characteristics of the various coating films in these two bands are shown in Table 2.
The radio wave characteristics of the indium coating "ECO MIRROR 49" are almost the same as those of the "base material without coating (standard)," indicating that it has very good radio wave transmission.
ECO MIRROR 49 Radio wave characteristics of the coating
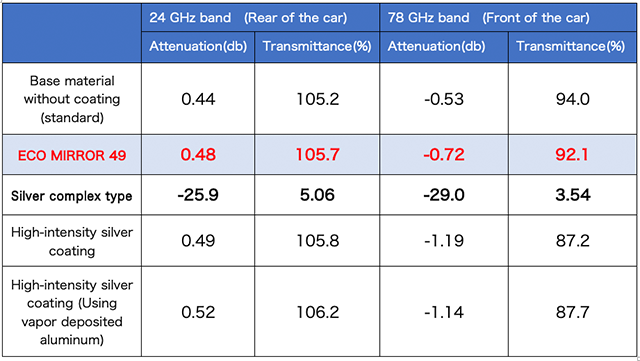
3. Why a rotating coating with R technology?
It has been found that in order to stabilize the mirror surface of the mirror layer, the mirror surface effect is maximized when the substrate is uniformly concealed and the film is as thin as possible.
(The thickness of the mirror layer is at the 400 nm (nanometer) level, as the indium paint should be able to cover it up.) Since hand-blown or net coating results in unevenness when thin coating is attempted, a coating technique capable of forming a uniform thin film is indispensable. In addition, since indium coatings are expensive, coating techniques that can be applied with as little paint as possible are also important.
Therefore, for the development of plating-like coatings for industrial applications, Takubo Engineering's "rotary coating with R technology" (see Figure 2), which enables mass production of ultra-thin film formation with a minimum amount of paint, is optimal and essential. This coating technique makes it possible to achieve uniform thin film formation at the nano-level. We believe that, in principle, it is extremely difficult to achieve nano-level uniform thin film formation and paint reduction with other coating methods.
- The machine shall be equipped with a syringe pump for fixed discharge. (See Photo-2)
- There must be a mechanism to control the ultrathin membrane in conjunction with a syringe pump.
- The spray gun must be equipped to apply multiple rings at the same time without variation.
- The system shall be equipped with control software that can change the discharge volume for each part.
- Software that allows numerical control of coating conditions and pursuit of paint usage shall be added.
Rotational coating with R technology
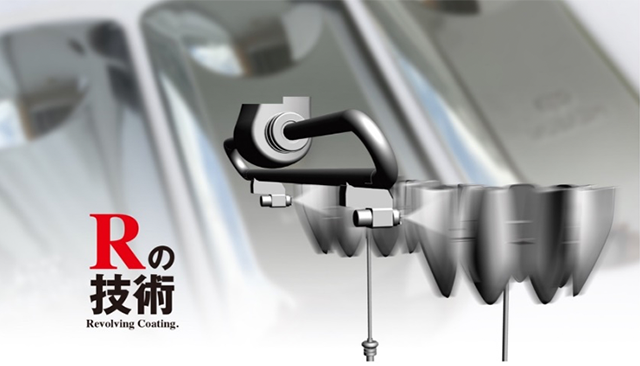
Syringe pump for fixed discharge
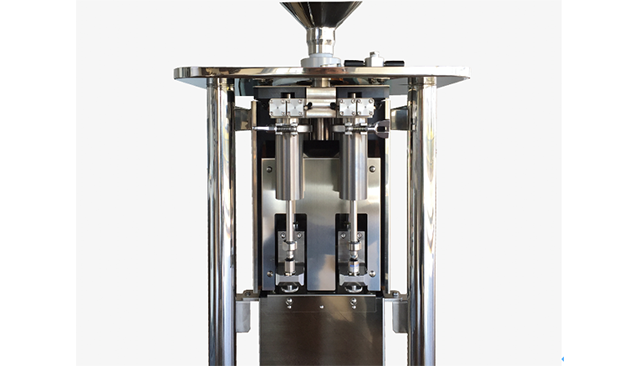
The basic process of In. Mirror Coating System is 3 coats and 3 bakes.
“Under coat → Dry →Indium coat→ Dry → Top coat → Dry”
The specifications of the In. Mirror Coating System are shown in Table 3.
Specifications of In. Mirror Coating System
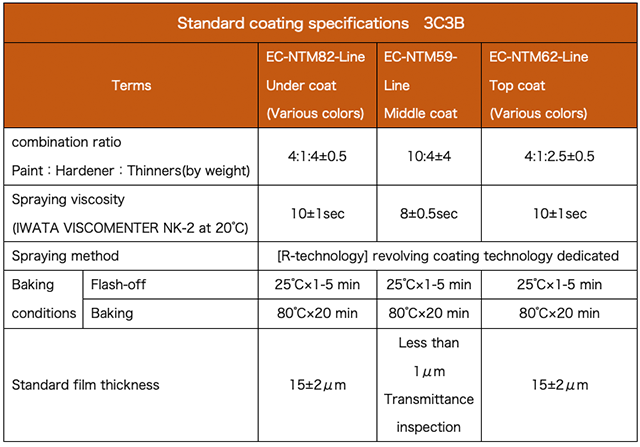
- ※Undercoat of EC-NTM82-Line is for general purpose plastic materials (ABS, PC/ABS, PC, PMMA).
- ※For light metals (Aluminum, Stainless steel, etc.), Super engineering plastics (PPSU, PPS, PEI, etc.), and Engineering plastics (Nylon, PBT, etc.), use EC-NTM86-Line Undercoat.
4. Teaching Assist Software “SWANIST”
“Rotating coating with R technology” is best suitable and essential for In. Mirror Coating System.
In addition, the teaching assists software “SWANIST”, which can manage and pursue paint consumption and make teaching easier, is also important.
“SWANIST" quantifies coating conditions and makes it easy to set and control coating conditions, enabling uniformity and mass production of ultra-thin films (refer to figure 3). The number and placement of workpieces are also important to minimize coating costs by reducing paint consumption to a minimum. “SWANIST" allows users to intuitively manipulate the angle, position, and number of workpieces in a 3D virtual space while examining and confirming workpiece placement. In addition, workpiece placement information can be shared and placement data can be transferred for jig fabrication (refer to figure 4).
Teaching assists software “SWANIST”
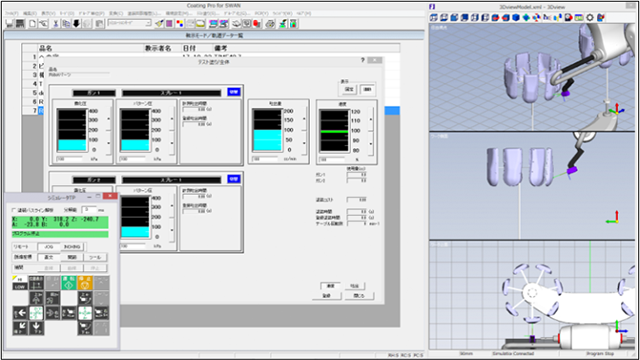
Workpiece placement setting screen
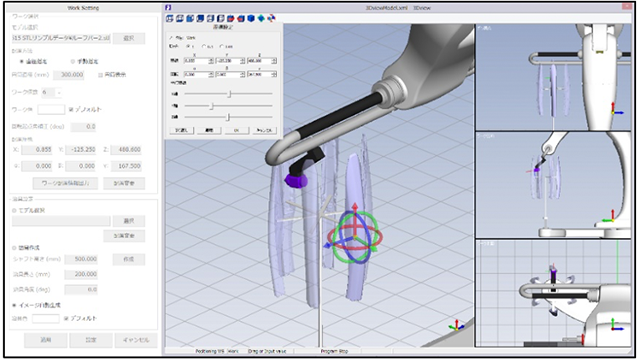
5. The layout of equipment dedicated to In. Mirror Coating System
The coating robots for the In. Mirror Coating System are the mass-production type LINE _DANCER (shown in Figure 5) and the general-purpose type SWAN_PRO. In addition, 4 basic styles of In. Mirror Coating System are standardized according to production volume. The production of each coating system is shown in Table 4.
Dedicated systems and production volumes for indium mirror coatings
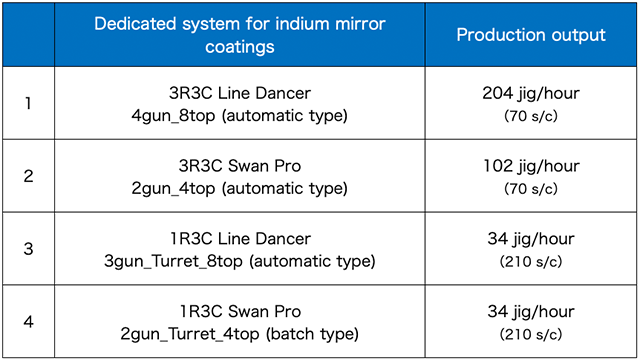
The layout of the 4 standardized coating systems is shown in Figures 6 through 9, but various systems can be proposed based on requirements.
- 3R3C Line Dancer 4-gun 8-top automated coating system for mass production
Figure 6 3R3C Line Dancer 4-gun 8-top automated coating system - 3R3C Swan Pro 2-gun 4-top automated coating system for semi-mass production
Figure 7 3R3C Swan Pro 2-gun 4-top automated coating system - 1R3C Line Dancer Turret 3gun4top batch coating systems
Figure 8 Line Dancer Turret 3gun4top batch coating systems - 1R3C line dancer 3-gun turret 4-top automated coating system (for small-lot, high-mix production)
Figure 9 1R3C line dancer 3-gun turret 4-top automated coating system
The environment surrounding the coating industry is changing day by day, and in recent years, it has become imperative to respond to the environment. In addition, market demands are increasing, such as the need to respond to the sophistication of automotive electronic components and home appliances. The rich mirror surface design and radio wave permeability functions of indium paint can now be fully applied to industrial applications through rotary coating with R technology.
Partnerships are also necessary to achieve advanced technological development. We hope to continue to contribute to solving social issues by closely coordinating and collaborating on coatings and coating systems that respond to the changing times and environment through the latest technology and software.
Monthly Coating Technology Published in December 2022 Created and authored by RIKO Publishing Corporation・Takubo Engineering Co., Ltd.